A resource blog for Industrial Designers that posts video tutorials and other useful things from across the web.
Friday, 31 May 2019
Fusion 360 — Use PDF for better Designs — Ask LarsLive by Lars Christensen
-- ► Subscribe to My Channel Here https://www.youtube.com/subscribe_widget?p=cadcamstuff -- Use PDF for better Designs is a snippet of Sunday's Ask LarsLive. You Can watch the full episode here: https://youtu.be/oo8sYo9ID3k (The advice in my videos are my own and are not intended to represent the views of my wife, children or employer) My email: lars.christensen@autodesk.com Want to learn more about Fusion 360? Check out this link: http://autode.sk/2rXApL2 Free CNC Handbook: http://bit.ly/2c2ivku LET'S CONNECT: https://twitter.com/Lars_cadcam http://bit.ly/2J3nP9k http://bit.ly/2jSQ3I3 MY BLOG, cadcamstuff.com: http://cadcamstuff.com/
View on YouTube
Unusual Product Design: Functional, Technology-Free Wearables for Fine Artists by Rain Noe
As a jaded and longtime design blogger, I rarely encounter a new-to-me product category that seems genuinely useful. But recently I found one such class of objects and, within them, an exemplary version that I'll show down below by a fellow named Frazier Price.
The category of product I'm talking about are body-worn palettes for painters. These are functional, technology-free wearables for artists working on-the-go, or even whilst in transit. Internet forums for painters are awash in DIY examples, like this simple one fashioned from a piece of wood or Masonite:
Image via Svyatoslav Brakhnov Academy of Realist Art
This design features a lid and a wristwatch-style band:
Image via: Svyatoslav Brakhnov Academy of Realist Art
Pigments can even be stored in something as small as a ring:
Image via: Svyatoslav Brakhnov Academy of Realist Art
While fabricating a ring is beyond the capability of your average tinkerer, the wristwatch form factor lends itself well to DIY. Dutch artist Koosje Koene is the co-founder of Sketchbook Skool, an online drawing/painting academy, and her handy father Frans Koene created this Watercolor Watch for her:
You can see a video of Frans demonstrating how he made it here.
For those who would like a similar object but don't want to make it themselves, Adventurous Art Supply sells a couple of variants on Etsy for around $25:
Even mass market retailers have offerings in this arena. Walmart sells this Van Gogh 12-Pan Pocket Box Watercolor Set:
Image by Trikist on the Wet Canvas forum.
Going back further in time, we find this intriguing example below, which has a story behind it. Watercolor painter John Haywood recently stumbled across, and purchased, this brass box stamped "Frazier Price Palette Box" that unfolds into a functional palette complete with rinsing wells.
Image by John Haywood
"I came across this sketchers' palette quite accidentally and had never heard of the make before," Haywood writes. "The fact that it was brass, boasted enameled mixing surfaces, and like nothing else I'd seen before certainly got my attention."
Curious about the box's provenance, Haywood poked around on the internet until he came across a forum--and found exactly what he was looking for, a post from Frazier Price himself explaining how and why he designed it.
Subject: RE: watercolour palettes
I have recently read the group's comments on palette boxes and mention was made of the Frazer Price Palette Box – probably time that I enter the forum as I am Frazer Price. I designed and had the box manufactured, in Shropshire, and first came on sale in 1985 and continued to be marketed until the early '90s.
Image by John Haywood
The box came into being because of my frustration with what was available for the travelling watercolourist. I was a publisher and whilst I was travelling extensively for Newsweek I would find time to sketch in one country before spending endless hours on my way to the next port of call and decided my time could be usefully spent by painting on the plane.
Image by John Haywood
I had a Gabbi box which was Ok but with only a curtain ring as a holding device it was uncomfortable. Therefore, over time, I designed a lacquered brass bijou type box just over 4? long, under 3? wide and 2? deep.
Image by John Haywood
The inside pieces were made from washable plastic with room for 18 half pans or with slides for paint from tubes, a water bottle and a divided reservoir for clean and dirty water. Two fold out enamel mixing trays one with a thumb hole enabling the box to be held comfortably as as a palette.
Image by John Haywood
It was launched in the Leisure Painter in 1985 and the advertisements had an endorsement by Rowland Hilder-the only time the great man endorsed anything- the selling price was £28.95 and with a couple of price increases it was marketed until '93/4 selling over 5000 boxes worldwide. It was also branded and marketed by Talens and Daniel Smith in the States.
Image by John Haywood
A point of interest when the box was first produced- the prototype costing £1,400.- I offered it to Windsor and Newton who initially showed great interest but then pulled out as they considered the box too 'glamorous' but asked if I would mind if they produced a plastic box based loosely on the FP box. I had no desire to go into mass production – hence the Cotman box* arrived on the scene.
Image by John Haywood
…All that's left now are a dozen boxes for the grandchildren and posterity. All my painting comes from the Frazer Price Palette Box and if you have the time click onto http://www.frazerprice.shutterfly.com and you'll see it at work!
*[Editor's note: The "Cotman box" Price refers to is, today, this commercially available design by Winsor & Newton.]
On his blog, Haywood mentioned a modern-day producer of portable brass-clad palettes, House of Hoffman. I looked them up and their products, designed and manufactured by a gent named L. Henry Fanelli, are pretty nifty.
The Sketcher I by House of Hoffman
The Sketcher I by House of Hoffman
The Sketcher I by House of Hoffman
The Sketcher I by House of Hoffman
Their prices are also quite dear--the Sketcher I shown above rings in at $1,225.
Lastly, when I was looking at this detail photo of Fanelli's fold-down, patent-pending "Thumb Hanger" for holding the box…
…it occurred to me that a body-worn palette would really be an ideal first-year industrial design school project. Here's why I say that:
- The object has clear utility for the end user, and very specific practical requirements
- It requires some human factors work for the interface (i.e. how do you securely hold it?)
- It's small enough that a student could manufacture a prototype in the school's shop
- The extant examples of this object span from $15 plastic Wal-Mart objects up to $1,000-plus luxury items, giving the students a wide range in how they want to execute
- At most design schools, there are nearby Painting majors who could be interviewed and used for testing different designs, providing important feedback
I'd love to see the range of designs that an entire class of ID students would come up with. If you're an ID professor who can pull this off, please do let us know!
from Core77 http://bit.ly/2W0pVZh
via IFTTT
Thursday, 30 May 2019
Fusion 360 — Better Tracing a Logo or Emblem — Ask LarsLive by Lars Christensen
-- ► Subscribe to My Channel Here https://www.youtube.com/subscribe_widget?p=cadcamstuff -- Better Tracing a Logo or Emblem is a snippet of Sunday's Ask LarsLive. You Can watch the full episode here: https://youtu.be/oo8sYo9ID3k (The advice in my videos are my own and are not intended to represent the views of my wife, children or employer) My email: lars.christensen@autodesk.com Want to learn more about Fusion 360? Check out this link: http://autode.sk/2rXApL2 Free CNC Handbook: http://bit.ly/2c2ivku LET'S CONNECT: https://twitter.com/Lars_cadcam http://bit.ly/2J3nP9k http://bit.ly/2jSQ3I3 MY BLOG, cadcamstuff.com: http://cadcamstuff.com/
View on YouTube
Wednesday, 29 May 2019
Fusion 360 —How To Machine Dead End T Slot — Ask LarsLive by Lars Christensen
-- ► Subscribe to My Channel Here https://www.youtube.com/subscribe_widget?p=cadcamstuff -- How To Machine Dead End T Slot is a snippet of Sunday's Ask LarsLive. You Can watch the full episode here: https://youtu.be/oo8sYo9ID3k (The advice in my videos are my own and are not intended to represent the views of my wife, children or employer) My email: lars.christensen@autodesk.com Want to learn more about Fusion 360? Check out this link: http://autode.sk/2rXApL2 Free CNC Handbook: http://bit.ly/2c2ivku LET'S CONNECT: https://twitter.com/Lars_cadcam http://bit.ly/2J3nP9k http://bit.ly/2jSQ3I3 MY BLOG, cadcamstuff.com: http://cadcamstuff.com/
View on YouTube
Tuesday, 28 May 2019
A Triumph of Design--and Manufacturing: The Story of Cubipods and an Innovative Mold by Rain Noe
Any number of designers can come up with wondrous solutions that don't mean a damn thing if they cannot be manufactured economically and efficiently.
This is a story not only about clever design, but of the clever manufacturing technique that had to be invented in order to realize said design.
The Problem
Ocean waves have a way of beating the living shit out of coastlines. Since that's where our oceanfront properties, coastal roads and all-important ports are located, protection is needed.
Image credit: NOAA
The Solution
To defend coasts from flooding, countries around the world install breakwaters, also called revetments. These are collections of massive concrete blocks, dumped into the water and piled atop each other.
The idea is that the waves then slam into the breakwaters rather than the cargo gantries, vacation homes and margarita bars we like to place along the shoreline.
Two Problems With This Solution
1. Building a breakwater requires manufacturing thousands of concrete blocks. A concrete block is relatively cheap to make, but the problem is that all blocks secretly want to be Legos. What I mean is, when you first dump them into the water, they look nice and random and jumbled, like this:
That jumbled-ness is desirable. You want both space between the blocks, and a lot of randomly-angled surfaces, to better dissipate the force of crashing waves. But the problem with cubes is that over time, gravity and movement cause them to inevitably settle, lining themselves up like good soldiers:
You can see the problem. When the water starts to rise, this happens:
Now the blocks have simply formed a smooth ramp that mirrors the seabed, and the waves can once again come crashing up and over.
2. To solve the cubes-like-to-settle problem, revetment designers around the world have come up with all sorts of fun shapes to use in place of cubes. This is like the opposite of Lego, where you're trying to come up with a shape that ensures it's impossible for the pieces to neatly nest together. Here's a sampling of existing shapes:
The problem with any of these will be obvious to any of you with any experience with molds. Cubes are pretty cheap and straightforward to mold. But to create (and operate) molds that can produce any of those other, more complicated shapes above is freaking expensive. In fact, some of those forms above look like the winners of a design competition whose theme is "How complicated and expensive a mold can you design?"
A New Design Solution
So cubes are cheap to mold, but the blocks interlock. Studying this problem, Josep Ramon Medina and Esther Gómez-Martín, two researchers at Spain's Polytechnic University of Valencia, wanted to see if they could design a cube-like shape that had fear-of-intimacy issues and would not lay directly on top of a nearby mate. They came up with a shape called the Cubipod:
The protrusions on all six faces of a Cubipod help the blocks interlock, while preventing them from self-assembling.
For testing, Medina and Gómez-Martín produced thousands of scaled-down Cubipods and filled a model coastline with them.
They found that their new shape did indeed maintain the required irregularity.
A New Manufacturing Solution
Now we run into the problem a lot of designers encounter: "I've got this great new design, but how can I manufacture it economically?" To comprehend the challenge with Cubipods, we first need to understand a couple of things:
1. The logistics of shipping.
Let's say you set up a factory to crank out Cubipods; now how are you going to transport them to the site? Stacking perfect cubes on a flatbed is pretty straightforward; but Cubipods are specifically designed not to get too close to one another, which is great for breakwaters but horrible for fitting them onto a vehicle.
The obvious solution, then, is to manufacture them on-site. Which leads us to the second issue:
2. Understanding how conventional breakwater block concrete molds work.
Take a look at this mold, produced by Portugese manufacturer Carldora, for an X-shaped breakwater block:
To give you an idea of its scale, here's the same mold with the scaffolding in place. Workers must stand atop this scaffold in order to pour the concrete into the sprues:
To release the part, molds of this size and type open laterally.
Here you can see the same arrangement in effect with an H-shaped design for a breakwater block.
Due to the Cubipod's shape and desired on-site manufacturability, this laterally-releasing mold arrangement was "out of the question," says mold designer Antonio Corredor Molguero. A laterally-releasing mold takes up far too much of the limited space available to manufacture breakwater blocks on-site. Instead Molguero and engineering partner Carlos Fermin Menéndez devised a mold that releases vertically.
Once the concrete has set up, the base stays put, and workers swing open four hinged panels on each vertical face that release those pesky undercuts.
Then the entire mold is lifted straight up, releasing a fresh Cubipod.
You might say "Yeah, but then that means you'd need to have a crane on-site." Well, they already have cranes on-site--how do you think they lift the breakwater blocks and move them into the water?
With Molguero and Menéndez's space-saving mold design, multiple molds can be placed quite close to each other, as the releasing action requires little lateral space. That means a lot of Cubipods can be constructed quickly and efficiently.
Wait a Sec, Why are Cubipods Any Better Than Tetrapods?
If you're a civil engineering nerd, or have ever traveled to Japan, or are an industrial design student, you're likely familiar with Tetrapods. Japan's coastlines are littered with this type of breakwater block, and countless, sadistic Industrial Design Drawing 101 instructors forced us to draw these jack-like shapes in perspective, over and over again.
By looking at the Tetrapod's shape, you might reason that they use less concrete than a Cubipod, and that they too are released the same way, i.e. vertically. However, that's not commonly the case. Instead, a top cover that encircles the sprue, plus three circular hatches, plus the three large panels that comprise the top part of a Tetrapod mold, must be individually removed and pulled away to release the part.
This is fairly graceless and inefficient operation that you can witness here.
A Debate Question
I took a close look at Carldora's design for a Tetrapod mold. They've added a bit of innovation with this "Decompression System," which allows the three large panels and three lower hatches to be loosened--but all remain attached to each other as they release the part. They can then be lifted off as a single piece.
However, I believe the Cubipod's mold design is still better, at least from a business perspective. Why? Cost of manufacturing. Take a look at a Tetrapod mold alongside a Cubipod mold:
Supposing the cast blocks were of the same scale, which of those shapes do you reckon is cheaper to manufacture? It's debatable, but I'm guessing the Cubipod mold's flat (if more numerous) surfaces might win the day versus the Tetrapod's finer, curvaceous and more complicated form. But I am not convinced of this, and I'd love to hear opinions from other industrial designers or engineers in the comments.
Conclusion
Thanks to the Cubipod, SATO, the Spain-based coastal construction firm that Molguero and Menéndez work for, managed to reduce their breakwater construction costs from 15% to a whopping 45%, depending on the project. And for their efforts, the duo of Molguero and Menéndez--whom SATO actually lured out of retirement to work on the project, recognizing they needed his expertise*--have been named Finalists for 2019's European Inventor Award.
If industrial designers often go unsung, I'll say mold designers receive even less recognition, so I'm glad to see these two getting their due.
__________
*In the Hollywood movie version of this story, Menéndez quits his job after one of his molds plays a central role in some spectacular tragedy. He swears he'll never design another mold for the rest of his life, sells his belongings and disappears. Molguero tracks him down in some bar in a developing nation, and convinces him to come back for One Last Job.
from Core77 http://bit.ly/2QsIC73
via IFTTT
Great Industrial Design Student Work: The Attaché Folding Stool by Rain Noe
"There are some problems with folding furniture," observed mechanical engineer Chi-Hao Chiang, who left his native Taiwan to pursu...
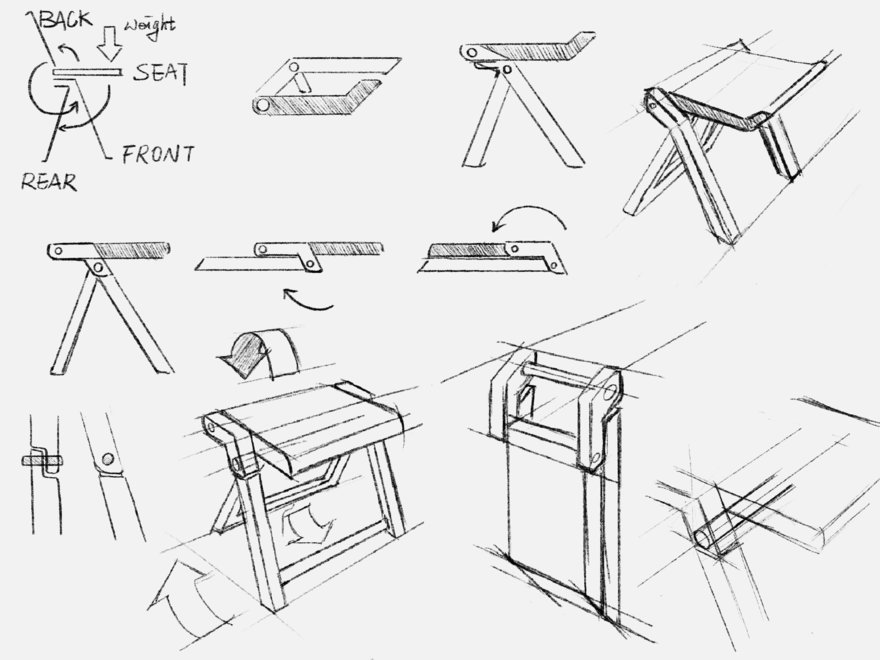
-
Laufer & Keichel , an industrial design firm based in Berlin, designed this Trailo desk for office furniture manufacturer Reiss . The...
-
If you're a "design lover" who likes to look at pictures of pretty objects, this roundup of posts is not for you. These are fo...