A resource blog for Industrial Designers that posts video tutorials and other useful things from across the web.
Thursday, 28 March 2019
When Product Design Meets Mechanical Engineering by Jimmy Huynh
When Industrial Design meets engineering My Portfolio https://ift.tt/2u820vK My Instagram https://ift.tt/2W4L31h Get The Pens Here: https://amzn.to/2GAA8sv https://amzn.to/2EgUg0c Metal Peg Board: https://amzn.to/2VyBBUj Peg Board Hooks: https://amzn.to/2SH85cY My Main Camera https://amzn.to/2GPaMrC My Microphones https://amzn.to/2Sqbcpv https://amzn.to/2CHqOjl https://amzn.to/2BQQXdM Microphone Setup Parts https://amzn.to/2ViLBAS https://amzn.to/2BQRix4 https://amzn.to/2VjFZq0 My Lights https://amzn.to/2Aq1DjE
View on YouTube
A Look at Six Car Design Specialties, Part 3: The Digital Modeler by
Two well-known specialties in exterior car design are sketching and clay modeling. These two skills are so longstanding in human history that you could pull Leonardo da Vinci out of a time machine, drop him into a car studio and he could do the work. But he'd have been baffled by what James Robbins does.
The Digital Modeler is the newest specialty in exterior car design, and in the past few decades it's become a crucial third leg that holds the tripod steady. The digital modeler not only helps shape both the early and final design of a car, but is responsible for coordinating with a dizzying array of departments, from design to engineering to marketing, to ensure that what comes out of the factory is exactly what the design team intended.
Digital modelers provide a level of speed, precision and support that any stylist or clay modeler from the Harley Earl days would have killed to have access to. Here in Part 3 of this series, we chat with Acura Senior Designer James Robbins, who describes his work with the Digital Modeling and Visualization Group. If you think of your average Autodesk user as a CAD jockey, Robbins is more like the guy who oversees the entire raceway.
Core77: Can you describe your position?
James Robbins: I'm a senior designer with the Digital Modeling and Visualization group here at Acura. Over the last seven years I've been very fortunate to work on cars like the NSX, both the 2012 concept car and the 2016 production car. I worked on headlight details and a lot of the surfacing for the Precision Concept. I was data project lead for the early design data of the 2019 RDX, and also worked on the RDX's production data.
What led you to become a car designer?
I grew up in New York on Long Island, in a really old house. My dad was always working on it, fixing things, tinkering with things. He was very fortunate to have my twin brother and myself his helping hands. He taught us about woodworking, how to replace doors and windows, install bath tubs, all that fun stuff. I think that developed my desire to tinker and make things. It also gave me an insight into how things work from a mechanical standpoint. That's a very much-needed skill, especially when designing something that's going to be made, something as physical as a car.
I got my car education from my grandfather; when I was growing up we'd go visit him in Scotland a couple times a year. He was into car racing, doing autocross in abandoned airfields and taking spirited trips around the Scottish countryside. As a 14-year-old that was extremely inspirational for me. He taught me how to drive manual on a right-hand drive car. When I was 16, I had to relearn it on the other side here, which is fun. That nurtured my joy for the automobile, and when I was 17 I started to autocross my CRX.
I think that everything combined helped guide my passions for design creation. And personally I'm interested in sketching, 3D modeling, 3D printing, VR technology. I'm very lucky that a lot of the hobbies I have overlap with my job. So it's very easy to come to work and do those things that I enjoy, and I'm always inspired by the designers around me and the creativity that they bring to their work. It helps us create these amazing designs.
Where did you go to school?
I went to the University of Cincinnati, where I studied industrial design with a focus on transportation design. There I excelled at 3D modeling and understanding forms and volumes. More importantly I learned, through class projects and internships, about design aesthetics and not only how to do 2D sketches, but how to translate them into tangible 3D models, whether clay or digital.
Robbins has owned multiple CRX's. Here he's modeled one just for fun.
Were your internships all automotive-based?
No, I was fortunate enough to have internships in packaging design, consumer electronics, soft goods and I worked on some body armor for a bit. It was a very broad spectrum of the industrial design field. I'm able to pull from a lot of those experiences and apply them to the work we do here at Acura.
What does your job here entail? From talking to [clay modeler] Matt Mantz we know that you and Matt go back-and-forth with stuff, but I'm not clear on exactly where the hand-offs occur.
[There are roughly] two different types of digital modeling we do. The first one is for early concept creation. This process typically happens alongside the clay modeling process while we're in development.
One of the first models we made for the RDX was capturing [Randall Smock's] sketch. Then we used the file to play with the proportions and the volumes here and there. Then that was given to Matt and he was able to use it as an underlayer base*.
[*Editor's Note: Robbins means that his digital file was sent to a milling machine, which carves a rough shape into a clay buck at 1/4 scale. Clay modeler Matt Mantz then begins shaping the form in clay. To understand more about this process, read Part 2.]
What kinds of software do you guys use?
We use a few different software packages here, but for the first part we use a polygon modeling/subdivision modeling software. It's mainly used in the video game industry and special effects for the movie industry. But I've been able to incorporate some of its workflows into our design process because it's very flexible in its approach to surface creation and modification. That's just one example of the software used; we have many that we use in the studio. We're very software agnostic, so whatever gets the job done.
Can you talk about when it's beneficial to do something digitally versus doing it in clay?
Whether we do something in clay or digitally--or both together at the same time--depends on everything from manpower to time to the scope of the project.
[With digital] it's very easy to make big proportional changes. I can grab a bunch of surfaces at once, and start manipulating them to, say, change the "speed" of the roof; I can change a tension point so that it's a little slower, a little higher, more aggressive, further back, whatever. Or we can change the wheelbase--even a 20 to 30 millimeter change to the wheelbase can really change the packaging of the car.
The software keeps the surfaces all combined and connected, so you don't have to worry about high-end surface continuity, tangency breaks and all that mathematical stuff--it's not important at this early stage in the process. It just lets us quickly test out all those things.
All of the mesh details and smaller things that require many iterations, we don't have the clay modelers do that. We can very easily do it using our modeling tools. We can make one spoke of a wheel and duplicate that 5, 7, 10 times, whatever wheel style you want, and we can do that really easily.
And obviously with digital, I have the ability to undo or [quickly return to an older version of the design]. That's great. This allows us to create more on the process so we can choose the best design.
Can you give us a concrete example of a time when working digitally made the difference?
One particular story I remember: Early on, they were considering a variation on the front end of the RDX. The variation required moving the front end about 30 or 40 millimeters. We were easily able to do that just by grabbing this data and moving it. A change like that really does affect the relationship of the hood to the windshield and the front volume of the vehicle, and even the cross-car feel. In this case we ultimately decided not to do it, and being able to look at that early on, and decide if [it's viable or not] is extremely beneficial.
And obviously, the benefit is being able to share this data with our clay team. We can implement the digital changes directly in the clay with the milling machine. So our clay modelers don't have to waste the time doing that by hand. Then they can spend the time really refining the highlights and the surfaces to move upstream in the process. They don't have to make the changes over and over again.
You'd mentioned there's at least two types of modeling. What's the second?
The next type is what I consider mock-up level or hard model quality data. We have an engineering team that does further refinements down the line, but our team does the design modeling. This is typically used to create internal mock-ups that are reviewed in the courtyard or even the concept cars. It's typically created a little later in the design modeling process, as the clay models refine. So we'll actually work with Matt and we'll get the scan data that he has, which is created by scanning his physical clay model. So then you can compare the two and make sure that the surface that you're creating captures the design that was refined in clay.
As one example, late in the process on the RDX, we needed to move that line on the hood quite a bit for some additional pedestrian safety and engineering requirements. So that was done in data and then verified on the clay later on.
Another thing we'll do is evaluate the surfaces by covering the digital model with what we call zebra stripes. This is when you're coming in and checking the continuity of the surfaces. The stripes help you see if there's a break in the surface, or really track how the highlights are going to flow across the body. This is also done in the clay modeling process, and all the way though the final stamped sheet metal, where they'll put a big panel with bar lights to replicate the check on the body side.
We also have other kinds of chrome metallic shaders that we can put on the digital model, that really shows the horizon line and how that's going to flow across the surface. You can use the shaders to look across the hood, making sure you've got nice, clean geometry that creates those nice highlights.
And this is always a back and forth process. We'll have our data checks weekly, as we decide to change and fine-tune things.
I'm assuming you guys go back and forth with the Spocks, the engineers, too?
Yeah so, for aerodynamics, we work a lot with our computational fluid dynamics team. Sometimes design changes are introduced that will affect the aero, and we're able to look at multiple iterations of the changes and see which one still looks good but meets the numbers. We work with our engineering team in Ohio to do that, it's a very collaborative experience.
Your group is called the Digital Modeling and Visualization group. What's the Visualization part?
So, we also use this software to break up the model into its components. We'll have the hood here, the fender, all the glass, tires, the mesh details all separated. As we get into the final part of our evaluation stage, which is the visualization, we can input that data that is broken up accordingly into its color chart, which we work with our CMF team to do.
The room that we're sitting in [the Digital Design Room] is where Dave [Marek] and all of our executives evaluate the model. We'll spin the model around on our turntable [virtually, on the wall-sized screen]. That way people can get a good sense of the vehicle with its actual color and material breakup. We can change colors on the fly, change the color of the cladding et cetera, and they can make sure the graphics look correct. They can go through all the different trim and color options to verify everything.
We can also change the environment that the car is in, for instance a studio background or a sunny tree-laden environment. We'll do completely different atmospheres for the vehicle. That way they can verify how the car would look in studio lighting, or parked on the side of the road under trees for a magazine shoot or something. We can do the pre-visualizations here before that gets all the way through to production.
It's interesting how many different facets of the process your group plugs into.
Yeah, I think that the biggest takeaway for the digital modeling side is we support the design team, the clay modeling team, and color and material (CMF). The clay modeling and digital modeling has a lot of overlap as far as surface creation and volume creation throughout the design process, but each has their strengths and weaknesses. So we try to leverage that throughout the whole process to make sure that we're using the right one when beneficial, so that we don't waste time. We want to create more designs faster, so we can choose the best design to represent our Precision Crafted Performance mission.
Although you're a "3D guy," do you still do any 2D sketching?
Oh yeah, we'll sketch as well. We can sketch with the other designers to explain how some things are not gonna work, or will work.
You mentioned that in school you covered the full gamut of ID skills, from 2D to 3D. What drew you to the digital modeling aspect of the design process? As opposed to being the clay guy or the sketching guy.
In design school I would draw all the time, but I was always more fascinated with the 3D side of it. I feel the 3D side, whether clay or digital, is where a lot of the design is done; I'm sure Matt mentioned it in his presentation. Because with the sculpting, creating those forms and translating that sketch is what makes the design, the design.
There are times when you can draw a great sketch and it looks cool, but the highlights aren't going to do [what they do in the 2D drawing]; that surface isn't possible or that corner won't work. So a lot of that has to be developed in 3D, whether it's clay or digital. They both complement each other. And my mind works in 3D, I see things in 3D when I'm drawing them. So I think that's what drew me to it. It's more tangible to me.
Obviously there's a place for the 2D sketch and for clay modeling. But you can offset a lot of the workload in 3D digital modeling, and that's great. It's very much a collaborative effort between everybody in the design studio.
___________________
Up Next: Thus far we've covered the three aspects of exterior design. But a car isn't much good without a fully-functioning interior and a cockpit that allows you to drive it, so stick around as we chat with the interior designers.
from Core77 https://ift.tt/2I2d6L1
via IFTTT
Saturday, 23 March 2019
Carla Diana on Embracing the Challenge of Creating a World for Both Humans and Robots by
In many ways, the technological future is upon us, but do we really know what it will look like? Designer, author, and educator Carla Diana is working at the intersection of industrial and interaction design to explore the impact of future technologies through hands-on experiments in product design and tangible interaction.
"Whereas designers typically use form, color, and materials to make an object express some human element...we're entering a time when sound, light, and movement are equally important parts of the creative palette," she notes in her seminal article Talking, Walking Objects which appeared on the cover of The New York Times Sunday Review in January 2013. Emphasizing the need for designers to take stock of the emotional value of robotics as much as any other product attribute, Diana's research aims to uncover new ways of making our everyday objects come to life.
Diana was recently appointed to create the 4D Design program at the Cranbrook Academy of Art, which will open its doors to the first class of students this Fall. Steeped in Cranbrook's history of experimental design, "the department explores the myriad ways that the physical world around us has become infused with an undercurrent of flowing data, turning everyday experiences into connected, feedback-driven interactions that are transforming every aspect of culture and society," according to their website.
A Cranbrook alumna herself (she also holds a degree in Mechanical Engineering from Cooper Union), Diana spent her early career as a Senior Design Technologist at frog design and designer for Karim Rashid. She went on to work with Smart Design for many years, where she founded the Smart Interaction Lab. In addition to her own studio work, she is an ongoing collaborator with the Socially Intelligent Machines Lab at the University of Texas, Austin.
Diana writes and lectures frequently on the social impact of robotics and emerging technology. She spoke at the first Core77 conference back in 2014, right after publishing LEO the Maker Prince, the world's first children's book on 3D printing. She currently cohosts the Robopsych Podcast, a biweekly discussion of design and human-robot interaction, and is coauthor of a forthcoming book on smart object design to be published by Harvard Business Review Press.
We recently caught up with the designer to learn more about her upcoming program at Cranbrook, how we can make sentient objects feel more human, and her vision for the "sweet spot" of robotics in the future:
Core77: Your new program is 4D Design. What is the fourth D, and why is it important?
Carla Diana: The fourth D is time. The program is focused on exploring critical questions about the world around us through creative applications of emerging technology. It includes everything from augmented reality to applied robotics and 3D printing, and the essence of it is around products and experiences that are responsive. The common thread is that all of these things will have the ability to change over time through intrinsic behaviors such as light patterns, sound, motion, and other dynamic displays. This is more important than ever as so much of our world is influenced by data flowing through it. We see it directly in the important role we give our mobile devices, but we can easily extrapolate to a future where this data flow is frankly present everywhere, from interactive spaces to wearable devices to networked autonomous vehicles.
"We need designers to better understand the implications of this future through tangible artifact and scenarios explorations."
Diana led the shell design of POLI, a social robot platform currently under development at the University of Texas, Austin in the Socially Intelligent Machines Lab run by Dr. Andrea Thomaz. It features camera recognition, a mobile base and a Kinova arm for object manipulation. Its body combines plastic shells with a soft neoprene body covering.
How did your design work and experiences influence your curriculum planning?
I have always been passionate about making the physical world around us interactive in some way. In my studio, I specialize in creative design for social robots. Earlier in my career, at Smart Design, I led very interdisciplinary teams that developed interactive products such as home appliances, medical equipment, and robotic vacuums. It was a thrill to bring together experts in engineering, industrial design, communication design and strategy to work on a product concept, and it also felt like these types of projects demanded a new kind of discipline that didn't exist yet.
When I branched out on my own with my studio, I also decided to take what I'd learned and create courses that synthesized all the seemingly disparate skills that need to come together to work on these kinds of products including storytelling, coding, projected images and displays, electronics prototyping and robotics. I launched the Smart Objects course at SVA, which has always been jointly run by the Interaction Design and Products of Design programs, and I also brought this course and others to UPenn and Parsons. The 4D Design department at Cranbrook is a chance to expand the philosophy of those courses into an entire program.
Diana's studio led the design of Moxi, a healthcare service robot developed by Diligent Robotics to autonomously complete tasks in hospital environments, allowing nurses to focus on patient care.
What makes this program different from other product design or robotics programs?
The key difference between 4D Design at Cranbrook and most programs in Product Design is our focus on interactivity and the creative application of technology. And we're different from most Interaction Design programs in that our projects will be based on object qualities, taking a holistic view of form, light, sound, and motion; many interaction programs have more of a focus on screen and app-based solutions whereas we will emphasize prototyping in the physical world. We will embrace applied robotics but are quite different from robotics programs in that we are at the epicenter of art and design, with a studio-based model. We will place value on the overall concept of projects, looking at how well they relate to the context in which they operate, placing high importance on societal and cultural relevance.
We will also be highly influenced by the other departments at Cranbrook such as Sculpture, Metalsmithing, Ceramics, and Fiber. For example, a student wishing to explore interactive textiles and wearable computing can draw on Cranbrook's rich history in textiles, going back to Loja Saarinen's historical design work. And a key difference between Cranbrook and most other programs is that we have no traditional classes, so instead of everyone having to meet preset benchmarks that may lose relevance over time, they will set individual goals based on their own career trajectories, diving deeper into the particular tools and methods that apply to their work rather than trying to cover everything in that short two year period.
Can you tell us more about the 4D Design Catalysts?
4D Design Catalysts are internationally recognized experts in the area of design and/or technology who will have an ongoing relationship with the program. They will work directly with students through lectures and workshops in active engagements that will take a variety of forms such as charrette challenges with specific design prompts, one-on-one critiques, studio tours, and targeted research projects. I'll be continually curating a list of Catalysts to represent a spectrum of current ideas and contribute to the collective voice of the program.
So far we have folks like Rob Walker, who will do a workshop with students to coach them on developing a point of view, and Bruce Sterling who will share his cyberpunk wisdom. Brendan Dawes has already come through campus to set the tone with his playful and experimental work in data expression. Joshua Walton is a Cranbrook alum and expert in augmented, virtual and mixed reality and works with James Tichenor to provide groundbreaking workshops. We've also got Nervous System to inspire us with their pioneering work in algorithmic form and digital fabrication. The innovation firms Tomorrow Lab and Jared Ficklin from Argo Design will provide a glimpse of product design solutions and business savvy. Emilie Baltz will encourage us to explore ways to engage the senses, and Zach Lieberman will look at poetic computation. We also have Matt Jones on board who has been part of many seminal experiments in tangible interaction and is now part of Google AI.
You've had a lot of experience designing and researching robotics. How did you originally get interested in robotics?
I think it all started when I was in high school and took part in a summer program that was run by a professor at NYU's Courant Institute. His name was Henry Mullish, and he was awarded a grant to teach computer programming to tenth graders. We started by learning how to encode punch cards and worked our way up to learning the syntax for five different computer languages, along with complex techniques such as sorting algorithms. I spent six weeks of that summer in a windowless basement surrounded by geeky kids like me and I loved every minute of it.
Since then, I always loved the magic of code, but I was also driven to make things. It was during my time in the 3D Design program at Cranbrook (yes, I'm an alumna!) that a light bulb went off in my mind as I realized that the physical and digital would soon become intertwined and decided to focus my career on exploring that vision.
The aim with Simon's shell design was to strike a balance between machine/appliance-like aesthetics and friendly, human-like characteristics. The robot also needed to appear youthful, suggesting a creature that is in a mode of continuous learning and observation.
Robotics entered my life quite a few years later when I was teaching at Georgia Tech in 2007. A professor named Andrea Thomaz was building a research lab to study how we might interact with computing devices in a natural way, using gesture and language instead of having to content with intermediary tools such as a mouse and a keyboard. She understood the importance of design and was looking for a creative partner to be part of the core team for a new robotics platform she was developing to study robot social interactions, so I jumped at the chance to join her team. The result was a robot named Simon that laid the groundwork for important research in human-machine interaction, and we have continued to work together on many robot projects over the past ten years.
The second evolution of Simon is Curi, named after Marie Curie and a reference to the word "curious." It has more refined facial features and, unlike the stationary Simon, Curi is mounted on a mobile platform.
A lot of your robotics work involves figuring out how to make them communicate in ways that people can relate to. We seem to be making slow progress in this regard, as opposed to leaps in sensors, processing speed, connectivity, and more. How do we make robots and other sentient objects more human?
I think one of our hangups in this regard is the fascination with making things literally mimic human behaviors, like text and speech. Instead, we can glean a lot about meaningful product design by exploring abstraction and striving for more poetic expressions of messages through light, sound, and motion. We have a tendency to be burdened by the history of devices, so it's hard to break us away from the devices we're accustomed to, like the mouse and the keyboard.
"From a business and marketing point of view, we get misled by the temptation to compete through improved specs and 'feature creep' when the real breakthroughs will come from understanding social mores and figuring out how to make products socially appropriate."
For example, the Amazon Echo has some lovely nuances, like the light that indicates the direction of the person it's currently listening to. But then it can go even further, like letting us understand and control when it's actively listening. Right now it's more like a spy that doesn't truly let us know what it's up to.
This is a topic that I'm squarely focused on right now as I'm co-writing a book with design research expert Dr. Wendy Ju on the social aspects product design for Harvard Business Review Press.
What sort of technology intersections are you most excited for your students to explore in the next few years?
Robotics in everyday objects, mixed reality, cyborg stuff (prosthetics and body augmentation), truth, wisdom, and privacy.
When users approach the Smart Coat Rack, it greets them current and upcoming temperatures as well as conditions such as rain, wind, and snow so users know what they'll need to face the day. A circular rack at its base balances the form with a space to keep umbrellas.
We noticed a lot of "companion robots" at CES—relatively simple objects that respond in cute ways and make you feel good. These sorts of robots seem effective, even helpful. Houskeeper robots, automatic breadmakers, laundry folding machines are large, complex, expensive, and seem to be WAY over engineered responses to 'problems' that ultimately don't work well. What is the sweet spot for robotics right now, and in the next few years?
I think the sweet spot will be in distilling robotic behaviors to only those behaviors that are meaningful in relation to the time and place they're in.
"Right now there are many new products that try to be what I call 'everything machines,' with multiple functions, tackling many contexts and offering all kinds of connected data feeds. My experience as a product designer has shown that successful products emerge from a focus on real and specific needs."
The Clever Coat Rack project is about this. It's made of wood, with embedded electronics. It has a full internet connection but instead of offering Twitter feeds and email alerts it just gives you the information you need at that moment when you're walking out the door: the current temperature, the day's high and low, and significant upcoming weather conditions. It offers what's needed to make a split-second decision about which coat to grab and whether or not you need an umbrella, but doesn't burden the moment with other interactions or decisions.
Some of the new Amazon housewares are starting to point that way, as well as products like the Jaxjox Smart Kettlebell that can track activity and offer relevant connected content. The Casper Glow lamp, for example, is a lovely product that captures the poetry and simplicity that I'm talking about, being designed with a focus on helping sleep through subtle changes in the glow it emits. It can be programmed as well as networked with other lamps. It's not trying to be a lamp for every purpose—all design decisions were in service to the sleep context.
from Core77 https://ift.tt/2Oop3Mc
via IFTTT
Friday, 22 March 2019
Design Job: Apple Inc is Seeking a CAD Sculptor/Digital 3D Modeler in Cupertino, CA by

Apple is looking for candidates with a strong interest and aptitude in digital 3D modeling for the Industrial Design group’s CAD sculpting team. Description The CAD sculptor creates high-quality digital 3D surface models used in the industrial design and product development process. Responsibilities
View the full design job herefrom Core77 https://ift.tt/2UMKpoT
via IFTTT
A Look at Six Car Design Specialties, Part 1: The Stylist by
"Just imagine being able to take a thousand different bits of metal; and if you fit them all together in a certain way, and then if you feed them a little oil and petrol; and if you press a little switch; suddenly those bits of metal will all come to life. And they will purr and hum and roar. They will make the wheels of a motor-car go whizzing round at fantastic speeds…."
That quote is from Roald Dahl's book Danny, the Champion of the World, where the young car-nut protagonist recounts his father's description of engines as "sheer magic."
A car engine is indeed a miraculous thing. So is the team of human beings that, like those thousand different bits of metal, must all fit together in order to create the car that surrounds the engine.
At the Acura Design Studio we were granted an in-depth look at how all of the different design departments contributed to the creation of their winning RDX. For the design student that's thinking about pursuing Transportation Design, this series should be an indispensable read. And if you're a fan of car design or industrial design, you'll enjoy this look at how an impossibly complicated multi-year design process all plays out.
We'll start with Randall Smock, the designer Acura tasked with translating the Precision Concept's spirit into the new RDX. As mentioned in the first article in this series, Smock would use the Precision as the "North Star" to navigate towards the final design.
Core77: Can you describe your position?
Randall Smock: I'm the exterior design leader for the RDX. I've been with Acura for 18 years and had the chance to work on a bunch of stuff, but my biggest project so far is the RDX.
What led you down the path of becoming a car designer?
Growing up in Arizona, I was always around cars. My father was a wholesale dealer, so he'd buy and sell cars constantly. It seemed like every day he'd pick me up from school in a different car. So I was really exposed to a lot of different types of designs and different brands.
More importantly, over time I could see how cars changed--although they were considered the same model. For example, I'd see a Corvette, and walk around it--"Okay, this is a Corvette"--and three or four years later, see the new model and ask "Why is it still a Corvette even though it's changed?" So I learned about this idea of DNA in styling.
And then you decided to study car design?
I actually didn't know that there was such a thing as car design. I knew that there was engineering, but not the idea of car styling.
When I was a sophomore in high school, we had to write a letter to a major company for an English class assignment. I wrote to GM and said, "Hey, I like Corvettes. I like cars. I like to draw…."
They actually replied back to me, with a lot of information--but most importantly, a list of schools that offered industrial design and specifically transportation design. That led me to ArtCenter College of Design here in Pasadena.
So being in Arizona, it was a quick flight to L.A. I came out with my mom. We saw the student gallery and I saw quarter-scale models. I saw hand drawn renderings and my mind snapped. I said, "This is it. This what I'm going to do. This is me, I can tell." So I had to finish high school, obviously, and went to junior college a little bit, and then made the switch to L.A. to go to ArtCenter.
Both ArtCenter and the Acura Design Studio are in Los Angeles. To what extent does the locale influence your work?
We're very accustomed to seeing premium cars and high-end sports cars every day here, and that's really inspirational--but it also gives you a craving, where you think "Okay, I've seen it. What else? What's next?" So it kind of drives your creativity.
What was your assignment with the RDX?
We were given the challenge to take the Precision Concept and apply it to an SUV--a daunting task, because the Precision Concept is a sports sedan and the RDX is an SUV; very different proportions. So we had to dig deep and identify that DNA that I was talking about, and fortunately the Precision Concept has very solid DNA.
During the RDX design process, the full-size mock-up of the Precision Concept was kept in the studio for all of the designers to refer to.
We wanted to think of this as a "sports sedan utility vehicle." So "SSUV" was an internal tagline that we used for it. We wanted to keep the sweeping cabin, keep the cross-contour surfacing from the Precision Concept. But to apply those things to an SUV, you have to have a really solid foundation. So that means the design has to be wheel- and fender-centric. All of the sculpting needs to sit very well on the wheels to make it look capable.
Smock's Precision-based rendering for the RDX.
Smock's Precision-based rendering for the RDX.
This mock-up [we're standing in front of] is what we would use later in the process. After we worked out all the feasibility numbers, we would build this, show our executives and say, "This is what we can make. We're ready to go if you can approve this." And they did, obviously.
This is the full-size mockup Smock refers to in the paragraph above. In person, it is virtually indistinguishable from the real thing.
[Editor's note: At this point Smock takes us around the mock-up, pointing out details and explaining the design decisions. Below, we'll insert photos of a production model and attempt to use images that correspond with Smock's talk.]
This is our achievement of taking the Precision Concept and applying it to an SUV platform. Starting with the prominent "diamond pentagon" grille. We had released [the grille] to the public already in the MDX, mid-cycle, but this time we could design the whole car with this in mind.
You can see the car really grows from this grill, whether it's the lines in the hood going from the corners, or the way that the jewel-eye headlights sweep and take your eyes from the center to across the car.
The daytime running light actually sets right on the fender to accentuate the stance.
Everything's a connecting device taking you around the car, and that leads you [around the side of the body] into this dance of lines, that cross-contouring that we were talking about.
Here's the fender line appearing and disappearing, the strong character line of the body side bisecting it, and then going above the rear fender. So everything's planted on the wheels.
Just like on the front with the headlights, the taillights nestle very well between these character lines and continue that motion around, and this kind of leads us to what we're calling the "dragon tail" taillight.
Early on in the development we actually didn't have this [design for the taillight], we were trying to be very avant garde with it and [have the light end abruptly], but it kind of disrupted the flow and we wanted to keep that motion going. So we brought the taillight across, onto the lid. We made a literal point, a dragon tail shape, to be that final exclamation to the statement that started from the front of the car.
We're all very proud of this, and it's doing very well [sales-wise]. We were confident with the design, and now the sales are proving the public loves it. I love it, I just got one a week ago in the white A-spec [trim]. It feels great to have been a part of it--but also to own it and experience it.
What role does manufacturability play in the design process? Do practical concerns force you into compromises?
The idea is that we want to take that [awareness of manufacturability] and design that into it, rather than recklessly designing something so super sleek that there's no chance it's going to get made. It's about pushing those limits: "How far can we push this, but still have everything be doable?
We do come into challenges, but we fight, we push. At one point we needed to heighten the bumper beam [for safety reasons] in the front fascia. It took a while to do that [and maintain the design], but we were persistent, we said, "We've got to keep this aggressive sculpted front end." We made it work.
Can you talk about how materials can influence design choices or options?
Sure, it depends on the materials you're using, of course, steel versus aluminum, and obviously plastics open up a lot of opportunities. For example, this is a completely resin tailgate, so we could make this whole thing in one piece. Usually you'll see a lot of cars where, in the back here, they'll have some kind of chrome trim or there's an extra line in here, because it's half-plastic and half-metal [necessitating a seam or cover-up]. This is all one piece of plastic so we can eliminate that, keep it really clean, more like the back end of an NSX. We wanted that performance car feeling and to get all of that sculpting. We couldn't get some of these radiuses if was steel.
Do you have a say in where the cut lines (the lines where the panels meet) go?
Absolutely. On the clay model, we actually tape on where we want the lines to go. We'll make that proposal to our engineers and they'll come back and say, "Well, you know there's a limit to how big the bumper is, so it can't be up to here," for example. And so we work within some limits, but it's definitely our say as to where we want these. We try to design them in and there's a reason [this cut line here] turns on that character line on the fender, rather than just mindlessly blasting straight through.
Let's say the line was here instead--
[Smock traces an imaginary line on the fender with his finger]
--then you'd have less plastic [in one piece], but then you'd have more metal [on the adjoining piece], and then what complications or challenges does that open up? It's a collaboration with the engineers, but in the end the designers make that proposal, and then we have a chance to tune them.
Not everything in a sketch or rendering can make it to production. What's the most challenging aspect of that?
Just the getting to grips with reality. What I find, though, in the production cars that I have worked on, I honestly feel that the car gets better as it settles into feasibility, and when they start to give us those limitations, it just looks more real.
This is the best the car has looked. We started off with [all kinds of] models and mock-ups, and I think this one still looks better. There's a lot of sculpting going on here for a very usable amount of internal space, and I have nothing to complain about on this one. I don't feel we compromised on anything, and we completely got the proportion that we want.
What was your favorite part of the project?
I enjoyed the whole process, honestly. As we kept going, it just got better and better and better. Sometimes if you do too much of an exaggerated theme early on you're going to lose something, but again, we started with such a strong base [in the Precision Concept] all we had to do was map that onto these proportions. The whole thing was the best part.
Up Next: After the Exterior Designer's rendering is green-lit, it goes to the next phase of design, clay modeling. Stay tuned!
from Core77 https://ift.tt/2UNJfJH
via IFTTT
Tuesday, 19 March 2019
Parameters, Joints, Layout Sketch & Glue — Everything in a Box — Fusion 360 by Lars Christensen
We will cover a lot in this video. Including the best Jimmy Diresta trick ever!!! So hold on to Parameters, Wood Glue, Joints, and Layout sketches.....This is wild!!!! Check out Jimmy Diresta's Channel: https://www.youtube.com/user/jimmydiresta My email: lars.christensen@autodesk.com Want to learn more about Fusion 360? Check out this link: http://autode.sk/2rXApL2 *It would not be the first time I have made a strong statement and been wrong :-) Ask my wife. Free CNC Handbook: http://bit.ly/2c2ivku SUBSCRIBE! https://www.youtube.com/subscribe_wid... LET'S CONNECT: https://twitter.com/Lars_cadcam https://ift.tt/2Cda02U... https://ift.tt/2jSQ3I3 MY BLOG, cadcamstuff.com: http://cadcamstuff.com/
View on YouTube
The Joys and Despairs of Visiting MoMA's "The Value of Good Design" Exhibit by
Since its inception, The Museum of Modern Art (MoMA) claims to have asked "What is good design and how can it enhance everyday life?" Made from a variety of materials—textiles, wood, plastics, leather, metals, glass, etc.—using then-innovative technology, 100-plus featured objects within MoMA's 2019 "The Value of Good Design" exhibit highlight the guiding design principles which shaped the tastes of worldwide consumers across generations.
Showcasing a global perspective, from a Brazilian bowl chair to a Japanese poster for a Mitsubishi sewing machine to a mass-market Italian Fiat Cinquecento to a Soviet-era East German Werra camera to an American shrimp cleaner and a propaganda film, MoMA selected pieces featured in past "Good Design" exhibits that demonstrated design's ability to reflect nations' respective and shared social and aesthetic values.
Passing Arthur Young's bulbous 1945 Bell-47D1 Helicopter (technically not included in the Good Design exhibit, though with it's plastic bubble made of just one piece, it should be) and instantly encountering Dante Giacosa's Fiat 500f city car, entering MoMA's "The Value of Good Design" feels monumental. Upon closer inspection, the exhibit design itself is nothing to write home about. With minimal flow, inconvenient physical pausing points for videos or projections, few object descriptions, etc., the exhibit caused me to wonder if its designers thought to apply the "good design" principles, printed on their walls and projected through their screens, to their spaces and experiences. Perhaps that will be something they will consider in their museum overhaul?
That is not to say the exhibit design was all bad. Standing in the middle of that space, surrounded by pieces—vacuums, furniture, pamphlets, tools, posters, tapestries, and more—whose design principles embody why I chose to pursue industrial design, filled me with joy.
"Since undefinable emotional factors as well as judgment play a part in what one likes, good design will always be different things to different people." — Betty Pepis, The New York Times, 1951
I was instantly reminded of my first year studying industrial design at the Rhode Island School of Design, facing assignments that filled me a mix of dread for and paranoia about my inevitable future of designing and creating enough plastic trash to occupy my own personal landfill. I was about to transfer, either out of my major or out of design school all together. Then, as a major requirement, I took Matthew Bird's class, The History of Industrial Design. Learning about the history of manmade things, about the manufacturing, material developments, and timelines that allowed the objects, furniture, and buildings surrounding me to be built in the first place was perhaps the most fascinating part of my undergraduate education. Deeply thankful for those lessons, I stayed.
But what about people who don't have that background? That education? That privilege? With many objects resembling those lining the shelves of Salvation Armies and Goodwills everywhere, and with most labels citing only the designer, object name, manufacturer, distributor, and years, how do visitors assign and understand the value of what's before them?
Without knowledge of and consequent passion for the "Tupperware Seal," borosilicate glass, furniture systems, and other niche industrial design history, visitors do not know what makes these pieces—pails, rakes, fishing rods, glasses, vacuums, shrimp cleaners, brooms, and other everyday objects—worthy of a museum pedestal. "I have never seen any useful object that could not have been done in innumerable ways, shapes and contours equally well-suited to its purpose," declared Eva Zeisel in 1946, according to the exhibit's rotating screen of "good design" quotes. In omitting information regarding the noteworthy aspects of a particular design, the institution leaves the viewer, unaware of the design's contexts, of which shapes and contours made the object museum-worthy. What responsibility does the museum—an educational resource—have to actually educate, to provide context and information?
"I have never seen any useful object that could not have been done in innumerable ways, shapes and contours equally well-suited to its purpose." —Eva Zeisel, designer, 1946
The exhibit's Good Design Lab, hidden behind a wall on the exhibit's far edge, serves as an opportunity for visitors to interact with some of the show's pieces.
MoMA aims for the exhibit to raise “questions about what Good Design might mean today, and whether values from mid-century can be translated and redefined for a 21st-century audience.” With that, I anticipated the exhibition to identify how and through what objects and experiences midcentury design principles are still relevant today. Yet, questions regarding what “good design” means today aren’t posed directly in the exhibit. At the most, it is clear what good design was. Perhaps for MoMA, a promotional powerhouse, “good design” is anything they can sell in their gift shops, as they invite visitors to explore “how, through its design stores, MoMA continues to incubate new products and ideas in an international marketplace.”
With very little separating “The Value of Good Design” from a glorified showroom shopping guide, to encourage the purchase of these products (though beautiful testaments to their times) today feels like promotion of the middle-upper class mass consumerism that is destroying the planet. I look forward to a museum exhibition that explores beyond the mass consumption paradigm, offering potential solutions and examples of what iconic, “good design” can look like in 2019 and beyond.
"The Value of Good Design" is on view at the Museum of Modern Art in New York City until June 15, 2019.
from Core77 https://ift.tt/2uaECh8
via IFTTT
Friday, 15 March 2019
Exploring the Dangers of Industrial Design Instagram Influencers by
A few months ago, a video emerged of Kanye West giving one of his signature verbal fire hoses to the students at Detroit College for Creative Studies. As I watched, a smile slowly curled on my face, anticipating the silence he would receive at the end of his rant.
That didn't happen.
I started to dig around, and I was shocked to see that generally speaking, students and graduates admire Kanye West. Remember, there's a very key difference between working with designers, and being one. Kanye is not a trained designer, but he's a creative mind that has the ability to pay designers to work on and execute his ideas. So then how did Kanye West become a design influencer that can do no wrong in the minds of design students?
All illustrations by Connor Pelletier-Sutton
I have a real love/hate relationship with concept of the "influencer" as a whole. I think it's magnificent that an individual's work can be collectively appreciated on a social platform, validating that there are thousands upon thousands of incredibly talented people out there viewing and interacting with their work. But the game has evolved so much from the dream we had 10 years ago, and it's fascinating (or quite frankly, upsetting) to dissect.
So let's start by focusing on Instagram, the clear choice for all types of creatives to share their work and watch an appreciative audience grow in front of their eyes in 2019. I joined Instagram back in 2011 while doing my masters in Architecture. "This is awesome!" I thought—a way to share my architecture models and ideas without bothering friends who wouldn't care about that on Facebook. And those filters, oh boy those filters. How wonderfully they would cover up the crappiness of my photos and quality issues in the models (or so I thought). At the time, "influencers" didn't really exist. The audience was small, and hash tagging wasn't a thing quite yet. We would mostly share our handles by word of mouth to one another, and the focus was on sharing our work. It was awesome.
Inherently, that hasn't changed—Instagram is still for sharing images. But as the platform gathered more users and it felt more and more crowded, we evolved with it. Whether intentional or not, Instagram today is a tacitly competitive space when it comes to creatives. It's as though we're all fighting for an audience that in actuality, can and does consume content from everyone. And out of this innate human need to compete and be the leader of the pack, we birthed influencers.
Now, it's not all bad. One of the greatest things to have come from this evolution is the desire to push ourselves and create better content to share, making us all better and hopefully encouraging others to push themselves too. Even this has its pitfalls, though, which lies mostly on the shoulders of influencers.
The problem here is that we're painting a complete illusion of what we do to the next generation of designers and reduce the job down to some beautiful renders or sketches.
One thing that social media influencers experience far less than a more traditional celebrity is the rise to fame through an in-person audience. That in-person experience helps others understand the impact of their actions and words, (positive or negative) more effectively than through only digital means. As a result, they may not necessarily think about the impact of their actions and how they influence others.
Let's take a minute to remember we're talking about creatives here, not socialites, movie stars, etc. Our influence and impact is minimal in the grand scheme of things, but our actions can be damaging in many other ways. I am not an influencer by any stretch, but on a near daily basis, I receive a message from a junior designer, student, or teenager saying something to the effect of "I wish I had your job!" Or "I hope to do what you do when I'm older!". But what nobody ever sees is all the work and time it took to get to there in the first place, and that's the danger.
A number of professional industrial designers use instagram as a way to detox from the reality of being a designer in the working world by sharing wild concepts, and beautifully rendered but essentially unusable designs, which in my eyes reduces them to sculpture. The problem here is that we're painting a complete illusion of what we do to the next generation of designers and reduce the job down to some beautiful renders or sketches. After all, who wants to see a photo of you on a bad hair day struggling to come up with an idea or paying invoices?
Even in my own line of work, I am not a traditional industrial designer. I often work on projects that are at times ridiculous and over the top. But because of social media, people have the illusion that I work on those types of projects all day everyday. What they don't see are the behind the scenes hours of PowerPoint, strategic meetings and tactical reviews I often go through see if the projects I propose will be actually be approved.
Now imagine then, the impact that someone with an even more significant following has on their audience? Whether they like it or not, everything they share or do will be consumed, and most likely, emulated. So do influencers need to be more mindful and conscientious? Absolutely.
However, plot twist: this isn't about them—it's actually about you. The clue to the power you as a "follower" hold is in the name we've given these people: influencers. Do you want to blindly follow and be influenced, or do you want to stop, take a minute and think about what you just saw or read, and decide if it makes sense for you to emulate?
That's not to say you should unfollow every industrial design influencer you admire. But I am saying that, especially when it comes to your current or future career, it's important to be practical and pragmatic with the loads of information you consume on a daily basis, whether it be via Instagram, YouTube or even design blogs. Take in the information for what it is—not for what you want it to be.
Remember the Kanye anecdote at the beginning of this article? It's understandable if you admire Kanye in some capacity as an artistic and cultural influencer, but please take his creative rants for what they are and avoid worshiping his every move, especially in a design context. Same goes for social media influencers within the industrial design industry.
from Core77 https://ift.tt/2T54aGn
via IFTTT
Thursday, 14 March 2019
HyperX Chargeplay Quad for Nintendo Switch Unboxing & Design by Jimmy Huynh
HyperX Chargeplay Quad for Nintendo Switch Unboxing Designed by yours truly ;) Chargeplay Quad for Nintendo Switch https://amzn.to/2F06zx5 Chargeplay Duo for Playstation 4 https://amzn.to/2T6dWYO My Portfolio https://ift.tt/2u820vK My Instagram https://ift.tt/2W4L31h Get The Pens Here: https://amzn.to/2GAA8sv https://amzn.to/2EgUg0c Metal Peg Board: https://amzn.to/2VyBBUj Peg Board Hooks: https://amzn.to/2SH85cY My Main Camera https://amzn.to/2GPaMrC My Microphones https://amzn.to/2Sqbcpv https://amzn.to/2CHqOjl https://amzn.to/2BQQXdM Microphone Setup Parts https://amzn.to/2ViLBAS https://amzn.to/2BQRix4 https://amzn.to/2VjFZq0 My Lights https://amzn.to/2Aq1DjE
View on YouTube
By Eliminating a Major CAD Drawback, SimSolid Gives Designers New Opportunities for Workflow by
We've just learned about a fantastic CAD tool—one that works with whatever CAD package you have—that will be a game-changer in the industrial design space. Altair's SimSolid is a simulation plug-in (also available as a stand-alone app) that completely eliminates meshing, that tedious process of simplifying geometry for Finite Element Analysis (FEA). By running SimSolid over your CAD model, you can do simulations nearly instantly—on your original geometry, with no clean-up required.
I know what you're thinking: "Isn't that FEA stuff for engineers? I'm a designer, why should I care about this?" To answer that, let's explain what has been the traditional FEA process up until now, then show you how SimSolid's new advantages would make a difference in your design workflow.
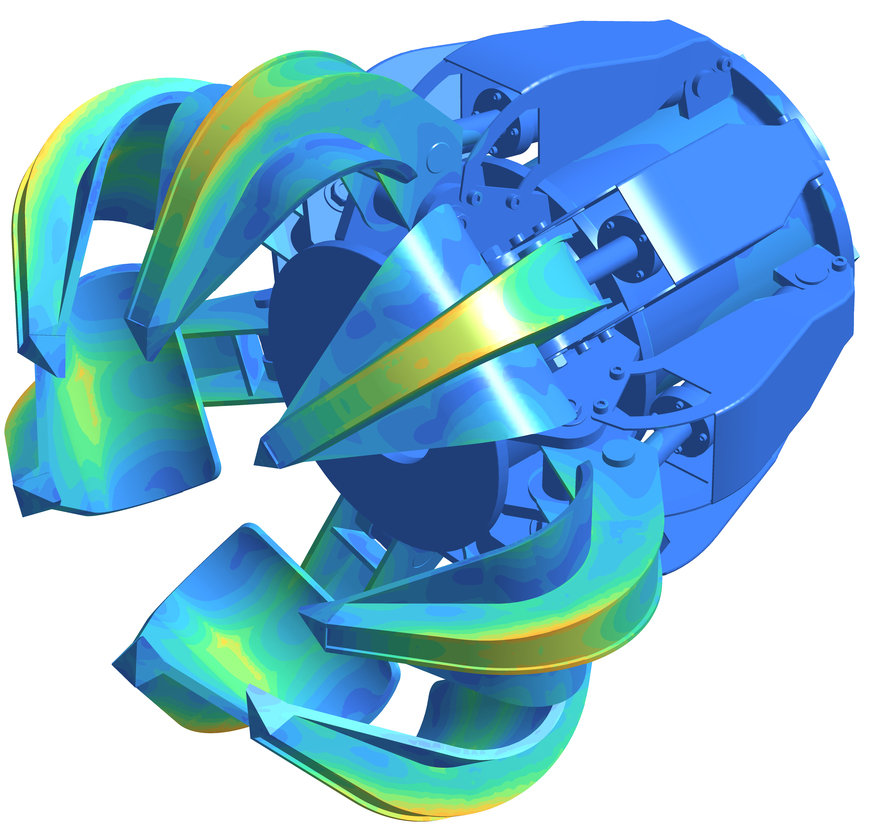
Traditional FEA: Useful, But Often Difficult to Use
Finite Element Analysis, or FEA, has become a crucial step in the CAD process. The more simulations you can do, the less prototypes you have to build, saving you both time and money. The problem is that no CAD program is sophisticated enough to run simulations on original CAD geometry, particularly with complicated assemblies, and requires the dreaded meshing step.
So traditionally, you'd design something and draw it up in CAD. It then goes over to an analyst or CAE department, where your CAD geometry is converted into a mesh so that simulations can be run on it. This geometry conversion is time-consuming and a bit of a black art: Should we run a coarse mesh for greater speed, and sacrifice accuracy? Or should we run a finer mesh for accuracy, waiting hours or even days for the computer to produce it?
Another problem with meshing is that it plays havoc with CAD geometry, creating extra busywork and providing opportunities for error. Often lost in translation during the meshing process are crucial connections, gaps and overlaps. Mating parts that you slaved over no longer line up precisely. Designs with small features, both thick and thin parts and/or irregular transitions all provide headaches that must be hunted down and re-worked. To save time, a common trick is to break your assembly into parts and analyze them separately. This introduces the opportunity for errors that can cost end users even more time down the road.
According to the website of one major CAD manufacturer, "Meshing a model is an integral step in performing any simulation. There's no getting around it—it has to be done." Well, with the arrival of SimSolid, that's no longer true.
SimSolid Simplifies FEA, Making it Easy for Designers to Use
SimSolid can run analyses nearly instantly—on your original CAD geometry. There's no meshing required; you pull your CAD file in and it's ready to go within seconds. You don't need to be an analyst with a background in mesh voodoo. You, the designer, can run simulations to figure out if your concept is even viable before kicking it over to ME.
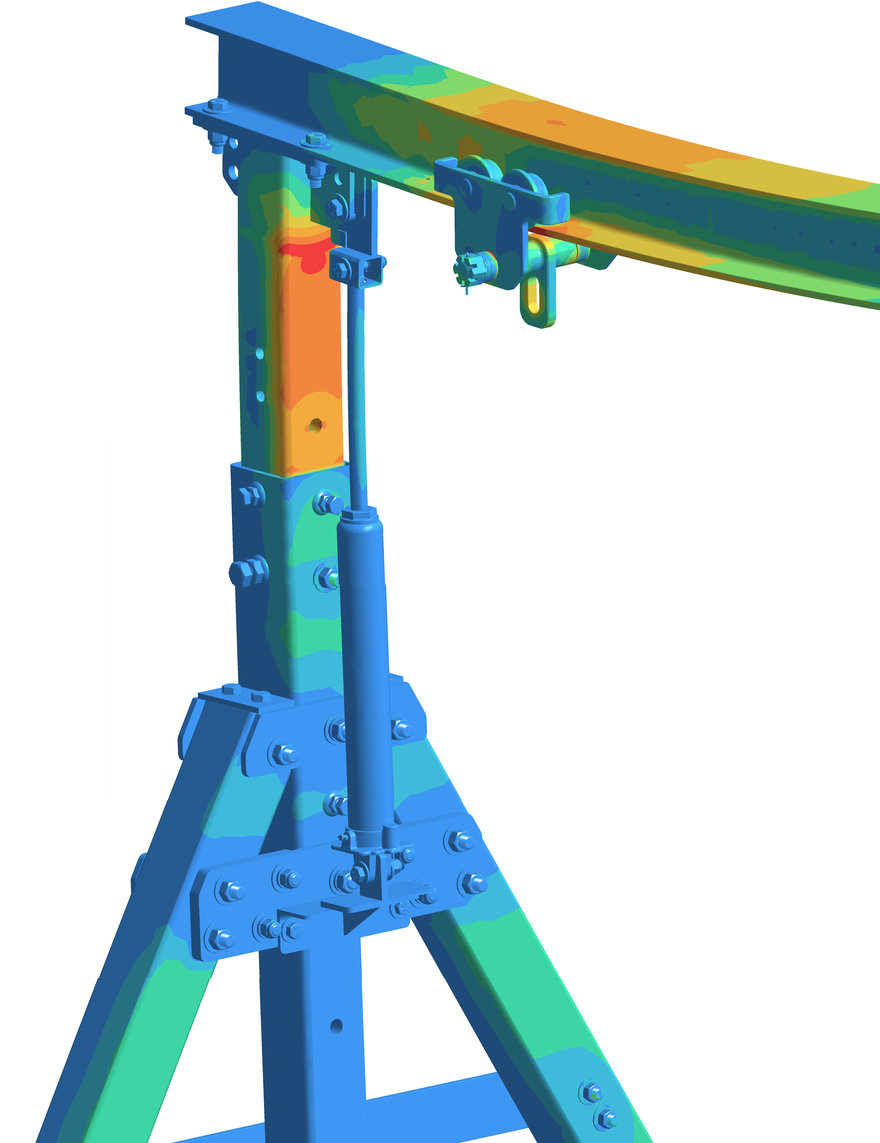
And if you're a designer working without the benefit of a dedicated engineering department—let's say you're a design entrepreneur or part of a small team crafting low-tech objects for a crowdfunding campaign—the utility of SimSolid should be obvious. Where is the clamp for your new bike light design most liable to break? Will your design for a cantilevered monitor stand support the 21.5 pounds of a 27" iMac Pro? Is the wall thickness for your object appropriate for the application? Are two mounting bolts enough, or do you need four?
To be able to see these results in seconds to minutes—rather than hours or days—can let you know, early on, if you're barking up the right design tree. And as you refine the design, having the ability to definitively see whether you're over- or under-engineering an object can give you a more accurate idea of BOM and eliminate that "Hey Kickstarter backers, sorry, but we screwed up" update down the line.
For a designer working within an organization that does have access to a dedicated engineering branch, SimSolid can provide an entirely new workflow. Even if ME ultimately needs to sign off after doing their own analysis, you can learn if your initial designs are viable well before knocking on their door. And by being able to spot problems early, you can tackle them with design proposals that hew more closely to your original vision, rather than you designing a unicorn and the engineers coming back with a rhinoceros.
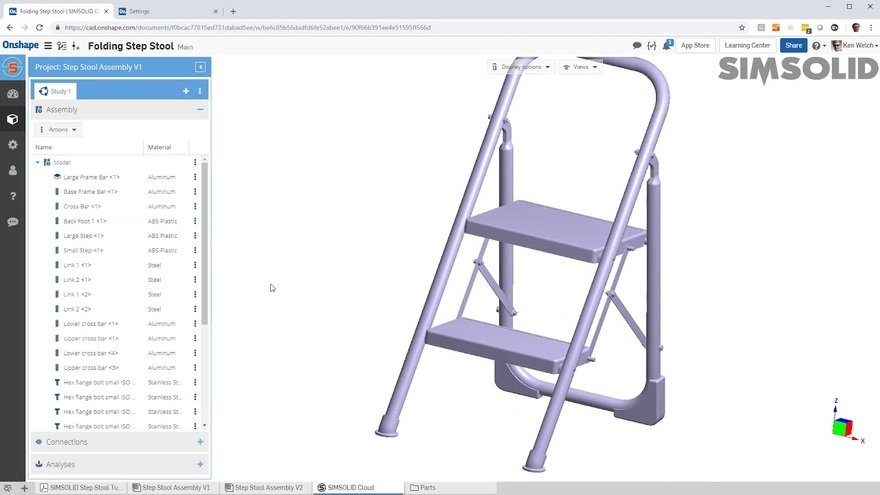
"SimSolid a very empowering piece of software for those users who were locked out of a part of the process; now they can participate," says co-developer Ken Welch. "Let's say you're an industrial designer, and you realize 'I can run a structural simulation right now, without having to wait.' Well, now you can ask a question, and answer it yourself.
"That allows you to develop your designs faster, because now you can use simulation as an integral part of the design process. When you have performance insights available to you early on in the design process, that opens up the possibility for new workflows that were simply not possible in the past."
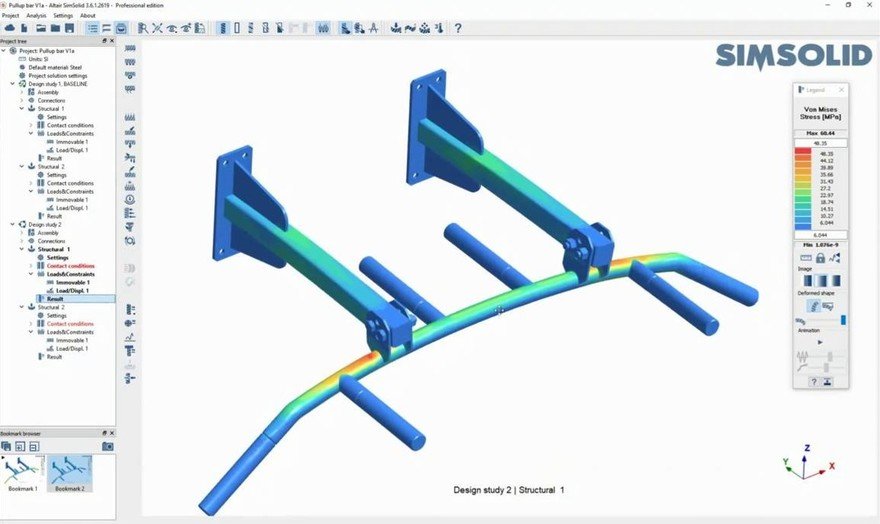
"And you can explore more. Not just with simple parts, as with most other FEA systems; with SimSolid you can look at full assemblies and very complex geometries."
Video Demonstrations
The following videos can give you a better idea of what SimSolid can do for you.
An Introduction to SimSolid
In this first video Warren Dias, Altair's Director of Global Business Developmen, explains the benefits of the software. This is the video you show to your manager:
Demonstration #1: Modal Analysis
Here you can see not only the multitude of CAD formats supported, but just how fast it is to pull a complicated part into SimSolid and run a quick modal analysis:
Demonstration #2: Comparing Multiple Design Variants
In this second demo, Dias r?uns a linear static analysis on two models, showing you how easy it is to compare them directly:
Demonstration #3: Performing a Non-Linear Static Analysis
In the third demo a non-linear static analysis is run, revealing separating contacts with as much ease as the first two demos:
As you can see, results are nearly instantaneous; that little flashing green bar at the bottom left of the screen seems to finish impossibly quickly. I noticed the same during demonstrations given to us by Welch, and I asked him what kind of high-powered hardware the program required.
"I'm just running it on a laptop," he explained. "A lot of people see the demos and think 'I need to run this on a supercomputer in the cloud, right? Or buy a really expensive GPU?' But no, I'm running this on a standard-core i7 laptop, and it runs great."
In short, SimSolid is fast, accurate, and doesn't require extra computing. It opens up a world of possibilities to designers working within today's fast-paced timelines, removing a barrier between ID and ME that seemed intractable. "Analysis never really had the impact it could," Welch says, "because it just couldn't work at the speed of design."
Well, now it can.
To confirm it yourself, you can try SimSolid for free. Altair has also launched a social media promotion where SimSolid users can post a simulation for a chance to win weekly cash prizes.
"Post your SimSolid simulation results to social media throughout the months of March and April 2019," the company writes, "and every week, five people will be selected to win $50 Visa Gift Cards. The best model at the end of the promotion will win a $1000 grand prize."
Click here for details on how to enter.
from Core77 https://ift.tt/2HeMDt9
via IFTTT
Great Industrial Design Student Work: The Attaché Folding Stool by Rain Noe
"There are some problems with folding furniture," observed mechanical engineer Chi-Hao Chiang, who left his native Taiwan to pursu...
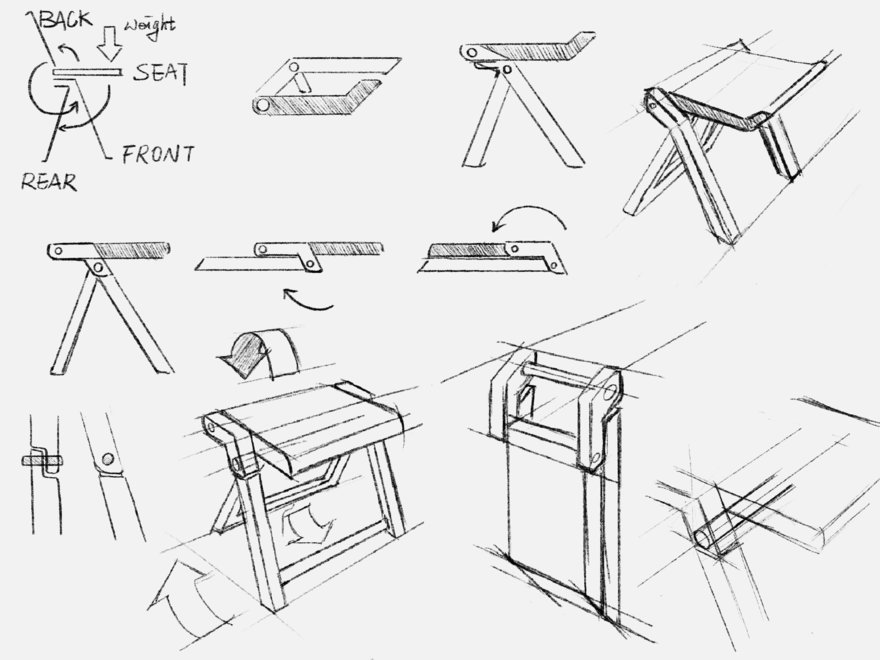
-
Laufer & Keichel , an industrial design firm based in Berlin, designed this Trailo desk for office furniture manufacturer Reiss . The...
-
If you're a "design lover" who likes to look at pictures of pretty objects, this roundup of posts is not for you. These are fo...